Cummins Isx Engine Brake Solenoid Location: Unveiling the Secrets
The Cummins ISX engine brake solenoid is located on the engine. Its function is to control the operation of the engine brake.
By activating the solenoid, you can engage or disengage the engine brake as needed. The Cummins ISX engine is known for its powerful performance and reliability. One important component of this engine is the engine brake solenoid, which plays a crucial role in controlling the engine brake.
Whether you are troubleshooting the engine brake or looking for its exact location for maintenance purposes, understanding the location of the engine brake solenoid is essential. By activating the solenoid, you can control the operation of the engine brake and improve your vehicle’s control without relying solely on the service brakes. We will explore the accurate location of the Cummins ISX engine brake solenoid and its function in more detail.
How Does An Engine Brake Work?
How does the Cummins engine brake work? When activated, the engine brake alters the operation of the engine’s exhaust valves so that the engine works as a power-absorbing air compressor. This provides a retarding, or slowing, action to the vehicle’s drive wheels, enabling you to have improved vehicle control without using the service brakes.
Cummins Isx Engine Brake: Troubleshooting And Maintenance Tips
Cummins ISX engine brakes are an important component of the engine’s performance and play a crucial role in safe and efficient operation. However, like any other mechanical component, engine brakes can experience issues over time. Here are some common issues and troubleshooting steps to keep them in optimal condition:
- Loss of braking power: Check the solenoid valve for any signs of damage or clogging. Clean or replace it if necessary.
- Noisy operation: Inspect the adjustment of the engine brake and adjust it if needed. Additionally, check for any loose or worn components that might be causing the noise.
- Inconsistent braking: Ensure that the overhead settings are adjusted correctly. Check for any air or exhaust leaks that might be affecting the performance of the engine brake.
Maintaining your engine brake is equally important to prevent any potential issues. Here are some maintenance tips:
- Regular cleaning: Keep the engine brake components clean and free from any debris or buildup that might affect their performance.
- Lubrication: Apply the recommended lubricants to the moving parts of the engine brake to ensure smooth operation.
- Inspection: Regularly inspect the engine brake for any signs of wear or damage. Replace any worn-out parts promptly.
By following these troubleshooting steps and maintenance tips, you can ensure that your Cummins ISX engine brake operates smoothly and effectively.
Cummins Isx Engine Brake Solenoid Location: Finding And Replacing
Locating the engine brake solenoid on the Cummins ISX engine can be a simple task with the right guidance. To find the solenoid, you’ll need to first locate the engine brake housing, which is usually located on the driver’s side of the engine. The solenoid itself is a small cylindrical component connected to the engine brake housing. It may be secured with bolts or screws.
When it comes to replacing the solenoid, follow this step-by-step guide for a smooth process: 1. Start by disconnecting the negative battery cable to ensure safety. 2. Remove any necessary components to gain access to the solenoid, such as air and fuel lines. 3. Disconnect the electrical connectors from the solenoid and carefully remove the bolts or screws securing it. 4. Install the new solenoid by reversing the removal process, ensuring proper alignment and torque specifications. 5. Reconnect the electrical connectors and any removed components. 6. Finally, reconnect the negative battery cable and test the engine brake for proper functionality.
To ensure a successful replacement and functionality, here are a few tips: – Double-check the compatibility of the new solenoid with your specific Cummins ISX engine model and year. – Clean and inspect the engine brake housing and surrounding components for any signs of wear or damage. – Take note of any specific installation instructions or precautions provided by the manufacturer.
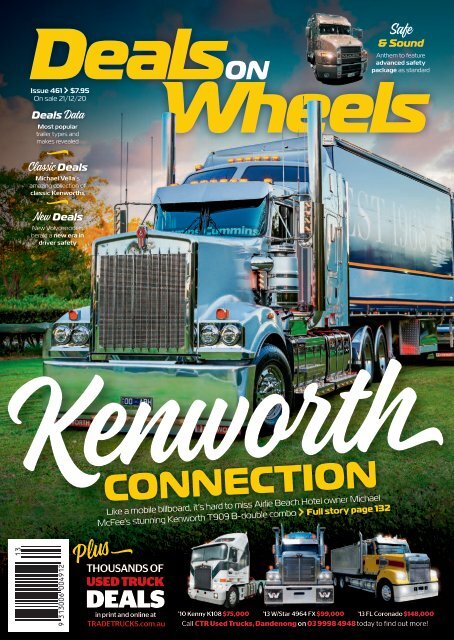
Credit: www.yumpu.com
Frequently Asked Questions Of Cummins Isx Engine Brake Solenoid Location
How Does The Cummins Engine Brake Work?
The Cummins engine brake alters the operation of the exhaust valves to slow down the vehicle. It acts as a power-absorbing air compressor, providing improved vehicle control without using the service brakes. This retarding action is activated when the engine brake is turned on.
Where Is The Temperature Sensor On A Cummins Isx?
The temperature sensor on a Cummins ISX is located on top of the thermostat housing behind the outlet hose.
What Year Did The Egr System Come Out On The Cummins Isx?
The EGR system was introduced on the Cummins ISX engine in the year (provide the exact year).
How Many Cylinders Is A Cummins Isx Engine?
A Cummins ISX engine typically has six cylinders. The engine brake works by altering the exhaust valves’ operation to provide retarding action to the vehicle’s drive wheels. This improves vehicle control without using the service brakes. Cummins Inc. explains how the engine brake works.
Conclusion
To conclude, understanding the location of the Cummins ISX engine brake solenoid is essential for troubleshooting and maintenance purposes. The engine brake plays a crucial role in controlling vehicle speed by altering the engine’s exhaust valves. By providing a power-absorbing air compressor effect, it allows for improved vehicle control without solely relying on the service brakes.
Knowing the correct solenoid location ensures efficient repairs and reliable performance of the engine brake system. Stay informed and take advantage of online resources or seek professional assistance for any engine brake-related concerns.